PURE PERFORMANCE
QUALITY - PURE PERFORMANCE
Pöttinger coating line technology incorporates cataphoretic dip priming and powder coating. Both these processes involve environmentally-friendly painting methods. No solvent is used in the mixing and application of the coatings.
Powder-coated paintwork has proven to be flexible and durable in the field. Neither sudden impact nor distortion will cause cracks to form once the machinery is in operation.
QUALITY COATING COMPOSITION
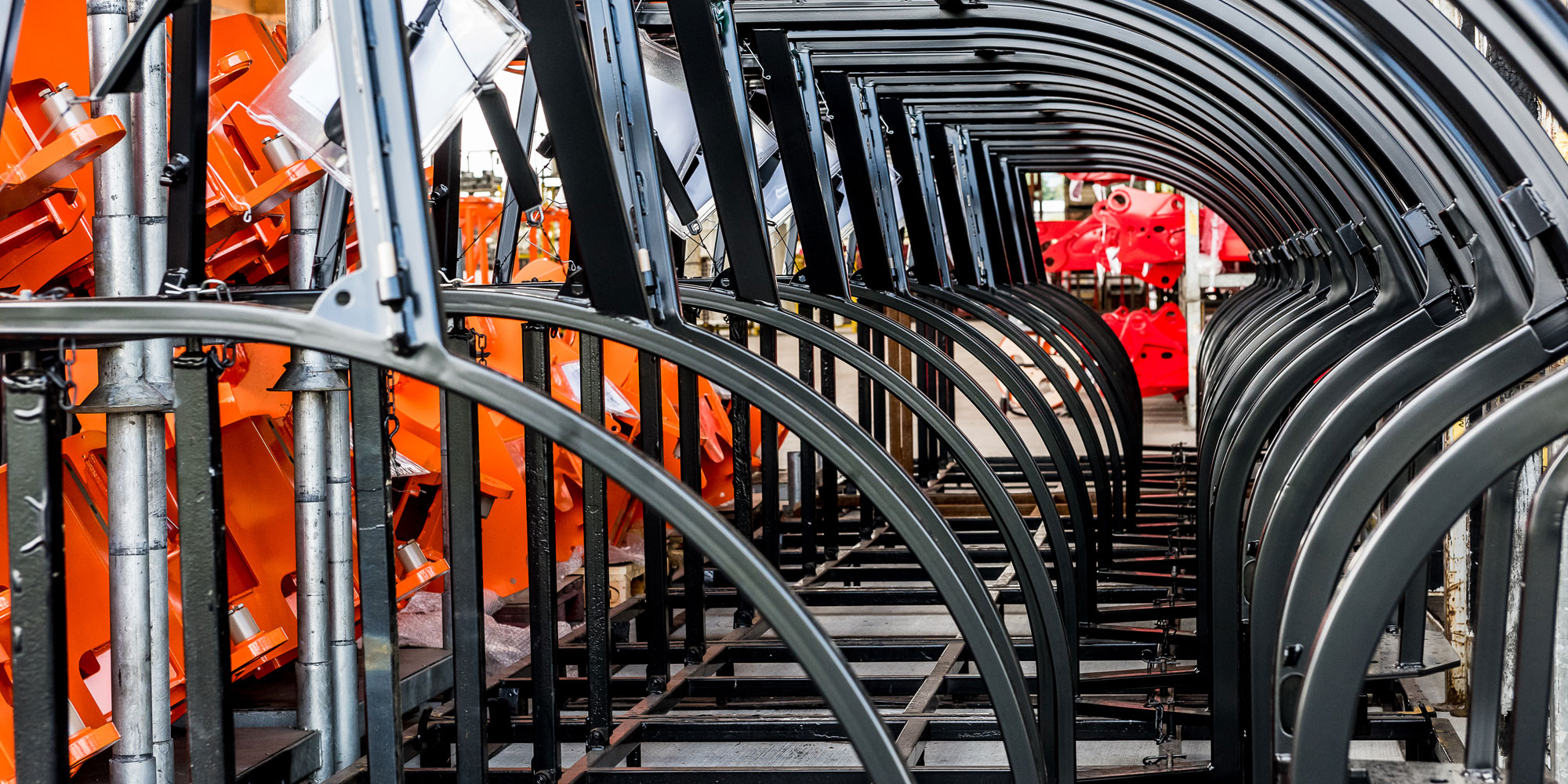
ADVANTAGES
You have the choice
The pre-treatment of components and various coating processes all offer different advantages. These advantages need to be taken into consideration when selecting the right process.
ADVANTAGES OF SAND BLASTING
Sand blasting is used to clean the surface and round-off the corners. Workpieces with a cross-section of 2 mm or more are sand blasted automatically.
A surface quality of up to SA 2 1/2 can be achieved as per ISO standard 8501-1. This process removes scale caused by laser cutting and welding, rust, coatings and contamination, to achieve the best possible adhesion of the coatings.
Full-power, medium-power or no sand blasting can be selected, depending on the material and level of contamination.
ADVANTAGES OF CDP
Compared to other painting processes - the advantages of this method need to be especially highlighted:
- Excellent corrosion protection
- Uniform layer composition
- All cravities are accessed without exception
- Environmentally-friendly process thanks to very low solvent usage
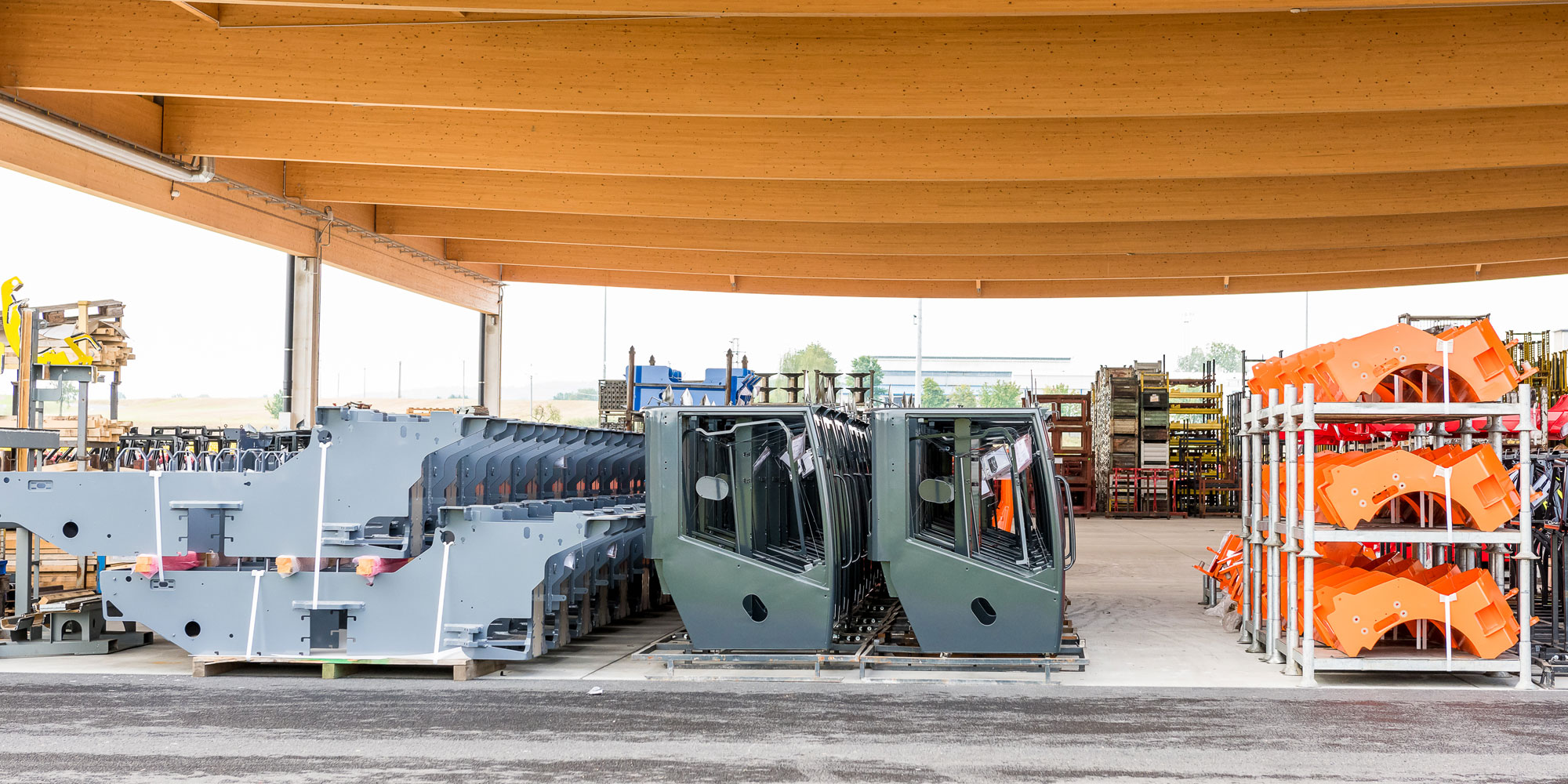
LOW ENVIRONMENTAL IMPACT
Both cataphoretic dip priming and powder coating involve environmentally-friendly painting methods. No solvent is used in the mixing and application of the coatings.
During powder coating the powder layer is applied by statically charging the powder material. 98% of the 'overspray' (powder that does not adhere to the workpiece) is recycled and used again.
Powder coating is one of the most economical and environmentally friendly painting methods.
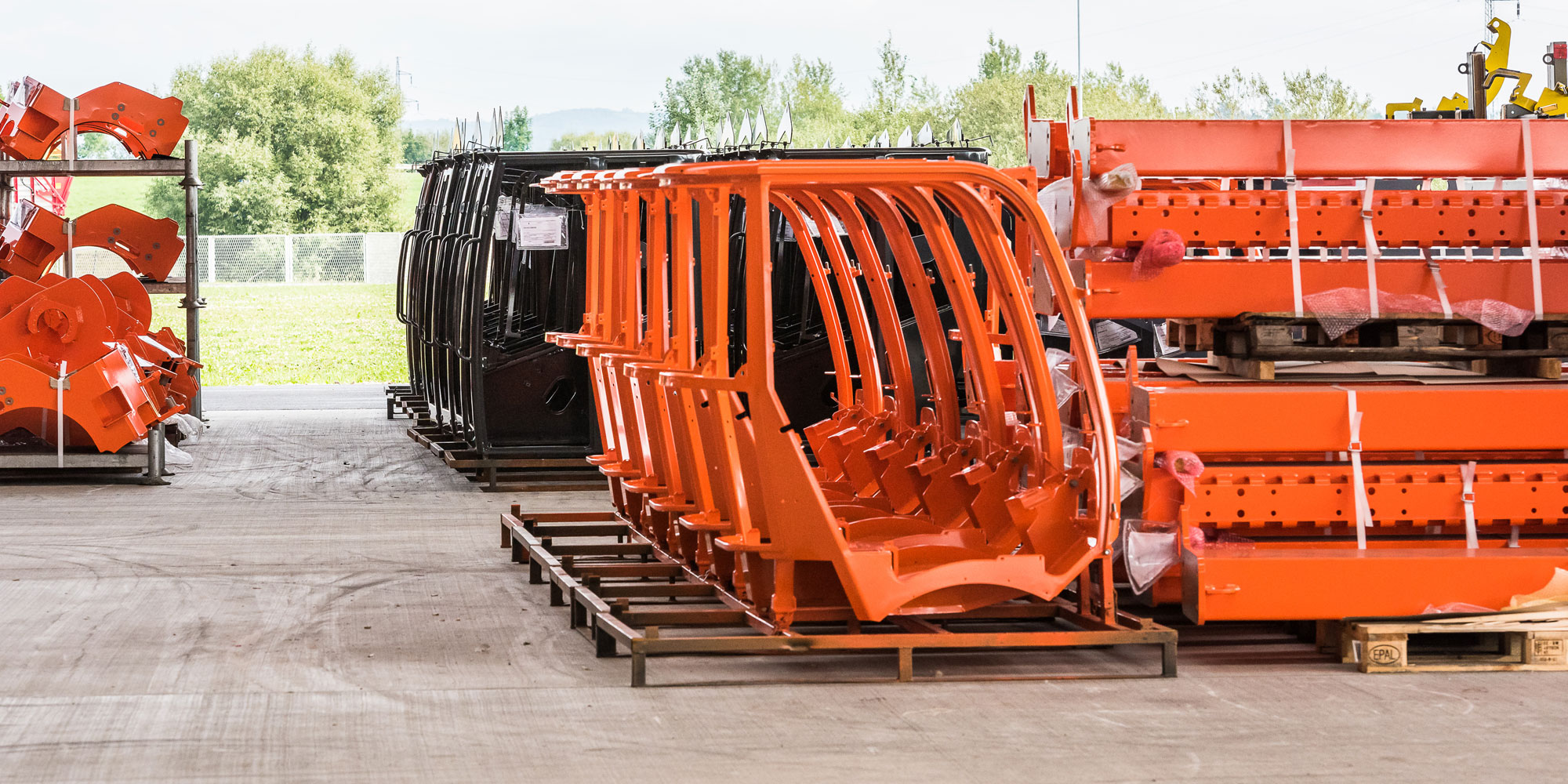
QUALITY TEST
The latest production processes for top quality.
Our coating systems are continually subject to a range of tests:
Salt spray test: DIN 50 021 and 9227
During this test, samples are continuously sprayed with a 5% salt solution at an ambient temperature of 35°C.
Duration of test: 1000 hours constant exposure.
Result: no blister on the surface, under rusting max. 1 mm along a deliberate score line. (St. Andrew's cross).
Cross-cut test: used as a quick test as per DIN EN ISO 2409.
During this test the samples are scored to a depth of 50µm with a series of crosses. The crosses are spaced at 1 mm on CDP samples and 2 mm on powder-coated samples. The resulting squares between the score lines must not break away from the surface. The results of this test produce information on the adhesion of each layer so the extent of damage can be assessed compared to reference samples.
Mandrel bend test: DIN EN ISO 1519
During this test, coated plate samples of a defined thickness are bent over a conical mandrel. This determines whether the coating is resistant to tensile and compressive stresses. The diameter at which the coating starts to crack or flake during stress testing is used as the reference value for the elasticity of the paintwork.
Coat thickness and gloss finish are also tested every day.